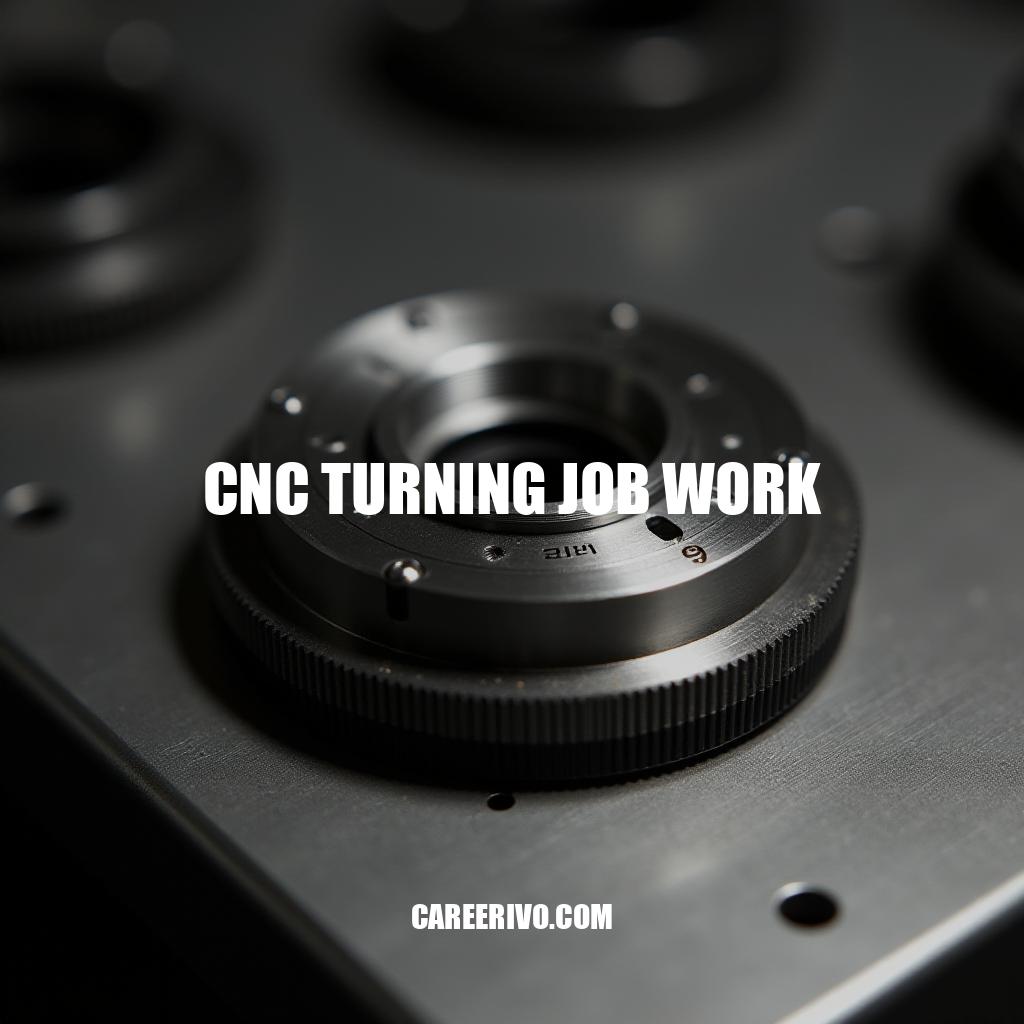
CNC turning is a way of shaping materials like metal, plastic, or wood using computer-controlled lathes. It’s a combination of old-fashioned mechanical skills and new-fangled digital technology.
The process works by fixing the material on a spinning axis while a cutting tool, guided by instructions, carves out the desired shape and finish.
CNC turning is great because it can make parts with very small details and tight measurements. Companies like those in aerospace, automotive, electronics, and medical equipment need this kind of precision to make things like turbine blades, engine parts, connectors, and surgical tools.
Process and Benefits
Step-by-Step Execution of CNC Turning Job Work
1. Material Selection:
The choice of material is crucial and depends on the application and performance requirements of the finished component. Metals such as aluminum, steel, stainless steel, brass, and titanium are commonly used, while plastics like ABS or nylon are selected for lighter applications. Factors such as machinability, thermal properties, and strength are considered when deciding on the material.
2.
Machine Setup:
-
Loading the Material: The raw material, usually in the form of rods or billets, is securely loaded into the chuck of the CNC lathe.
-
Programming: The CNC machine is programmed using G-code or CAD/CAM software to execute precise cutting paths. Details such as speed, feed rate, and tool movements are pre-defined to match the specifications of the component.
-
Calibration: The machine is calibrated to ensure exact dimensions and tolerances. Probes or trial runs are often used for this process.
-
Coolant System: The coolant system is set up to reduce heat and prevent material warping during cutting.
3.
Tool Selection:
The selection of tools depends on the complexity of the geometry and the material being machined:
-
Turning Tools: These are used for basic cylindrical shapes.
-
Grooving Tools: Employed for making channels or recesses.
-
Threading Tools: Utilized for creating internal or external threads.
-
Cutoff Tools: For separating the finished component from the stock material.
High-speed steel (HSS), carbide-tipped, or diamond-coated tools are chosen based on the hardness and machinability of the material.
4. Precision Cutting:
The CNC lathe rotates the workpiece at high speed, while the cutting tool moves along pre-programmed paths to create the desired shape. The machine performs operations such as facing, turning, boring, threading, grooving, and parting. Multiple tools may be used in a sequential process for complex designs.
5.
Finishing Techniques:
After the component has been machined, finishing techniques are applied to enhance surface quality and meet exact specifications:
-
Polishing and Deburring: Removes sharp edges or burrs for safety and aesthetics.
-
Surface Treatment: Processes such as anodizing, coating, or painting may be applied based on requirements.
-
Inspection: Dimensional accuracy and quality are verified using tools like calipers, micrometers, or CMM machines.
Advantages of CNC Turning Job Work
Efficiency: CNC turning machines operate with minimal human intervention once programmed, enabling faster production cycles and reducing downtime.
Repeatability: The programmed operations ensure that every component meets identical specifications, reducing errors and ensuring consistency in large batches.
Complex Geometries: With advanced tooling and precise programming, CNC turning can produce intricate designs, including threads, grooves, and delicate recesses, that manual methods cannot achieve reliably.
Contribution to Cost-Effective Manufacturing
Mass Production: CNC turning allows manufacturers to produce large quantities of components efficiently while maintaining high quality. The automation reduces labor costs, and the repeatability minimizes material wastage.
Customization: For small-scale or niche production, CNC turning offers the flexibility to create bespoke components without the need for extensive retooling. This is ideal for industries such as automotive, aerospace, and medical devices, where unique specifications are crucial.
Reduced Lead Times: With rapid setup and execution, manufacturers can meet tight deadlines without compromising on precision.
CNC turning continues to be indispensable for achieving precision, scalability, and innovation in modern manufacturing.
Its adaptability bridges the gap between large-scale industrial needs and specialized, customized projects.
CNC Turning Job Work: A Vital Component of Modern Manufacturing
CNC turning job work plays a vital role in modern manufacturing by providing unparalleled precision, consistency, and efficiency across various industries. Its ability to produce complex geometries with tight tolerances makes it an indispensable tool for companies requiring high-quality machined parts.
The CNC Turning Process
The process involves loading the material into the CNC lathe, programming the machine using G-code or CAD/CAM software, calibrating the machine to ensure exact dimensions, and setting up the coolant system. The selection of tools depends on the complexity of the geometry and the material being machined, with options including turning tools, grooving tools, threading tools, and cutoff tools.
CNC Turning Operations
The CNC lathe then performs precision cutting operations such as facing, turning, boring, threading, grooving, and parting, using multiple tools in a sequential process for complex designs. Finishing techniques are applied to enhance surface quality and meet exact specifications, including polishing and deburring, surface treatment, and inspection.
Advantages of CNC Turning
CNC turning offers numerous advantages, including efficiency, repeatability, and the ability to produce complex geometries. It enables manufacturers to produce large quantities of components efficiently while maintaining high quality, reducing labor costs and material wastage. Additionally, CNC turning allows for customization without extensive retooling, making it ideal for industries such as automotive, aerospace, and medical devices.
Benefits of CNC Turning Job Work
The benefits of CNC turning job work are numerous, including reduced lead times, improved consistency, and increased precision. As technology continues to advance, CNC turning is expected to play an even more significant role in modern manufacturing, enabling companies to produce high-quality machined parts with greater speed and efficiency.
Conclusion
In conclusion, CNC turning job work is a critical component of modern manufacturing, providing the precision, consistency, and efficiency required by various industries. Its adaptability and ability to produce complex geometries make it an indispensable tool for companies requiring high-quality machined parts. As technology continues to advance, CNC turning is poised to play an even more significant role in production processes, driving innovation and growth across multiple sectors.